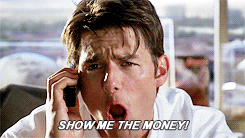
Where will we allocate the retrofit budget for our machines?
This question had been asked over and over, every year by one of our customers, a major player in the packaging industry.
Imagine the situation and even try to remember if it happens in your company: the CFO gathers 4 or 5 managers and launches this question in the room, projecting the budget for the following year. The industrial director made the same challenge with his factory management. And that’s where the “opinion fight” begins. (We like to say that without data, you are just another person with an opinion).
Each one brings his/her side, wanting the best for his/her line. But no one can prove why retrofit money should be allocated to a particular machine, since downtime and scrap data are difficult to gather without a proper system.
So, did you identify yourself within the situation?
In the past, the company used solve this situation in an unsatisfactory way: CFO, CEO and Industrial Director ended up dividing the retrofit budget into equal parts. This ends up not being an effective strategy, not even measurable in the medium term of the plant but at least it made everyone in the room more or less happy. unfortunately, companies are not here (just) to make people happy.
There was only one way to solve the situation: with data.
Choosing the right data
As usual, during those moments, many ideas surfaced. The first to emerge involved long implementation times, complex involvement of external consultancies and numerous phases until the final response was reached.
Another option was to hire new technology professionals to join the two internal developers and create a home-made solution.
The agreed solution came through one answer: we need a platform that is simple to operate and has an easy experience for users, whoever they are.
In addition, we need to discover relevant data from each machine, in each part of the line, and then take data by periods. “Only in this way will we be able to know which machine has had the best or the worst performance”.
For better understanding: the client of this case is a packaging company, specialized in manufacturing and printing of tubes and alveoli suppository. Currently exports about 80% of its production.
How did they achieve U$ 144k of capacity increase?
In the main dashboard, PackIOT allows customers to easily understand which lines/machines are responsible for the most impactful downtime and the most waste.
With this data in hand, mapped within six months, they were able to decide which machine would be worth the investment.
The directors then decided to choose the machine with the greatest impact in downtime and to focus on the retrofit of this equipment.
In this way, there was a targeted investment, so they managed to reduce 30% of this machine’s downtime.
In monthly terms, this operation represented a reduction of 120,000 tubes, which means an opportunity of increase productivity in 12,000 USD per month, or cost-saving, we can say so. (Before the reductions were 0.5% and the decision was questioned because they could not prove the real impact).
Taking action with data
Digital Transformation, Industry 4.0, IoT, all this is a lot of trends that must go through your screen every day.
The big secret of all this movement is to use technology to deliver more results in the factory and make people’s lives easier.
Broadly speaking, using technology in the everyday life of the industry is a never-ending path. As you saw in this case, imagine the impact that other data-driven decisions can bring to your business?
There are millions of dollars in cost reduction and opportunities for increasing revenue. This without forgetting the better quality in the work environment and in the life of the employees.
In addition, companies now have the need to develop a solid digital culture and ensure that the example comes from the top.
It is also imperative that they are able to attract, retain and build next-generation resources (so-called digital natives) or others, who feel comfortable working in an increasingly dynamic ecosystem according to PwC’s Global CEO Survey, the difficulty in getting the core competencies for the industry has been an indicator that has been increasing since 2013 (53%) until 2016 (76%). This is one of the challenges for the industrial sector.